The Challenge: Keeping Metal Plants Safe, Productive, and Profitable
The metal industry may seem like a traditional sector, but it’s rapidly embracing innovation—especially when it comes to safety and efficiency. Today, inspection robots in the metal industry are helping manufacturers modernize operations and address long-standing challenges.
As the backbone of global infrastructure, the metal industry supports everything from automobiles to construction and electronics. Yet behind this critical role lies a range of issues that threaten operational performance, workforce safety, and long-term sustainability.
For decades, manual inspections have been the standard approach to ensuring asset integrity. But as metal plants push for greater efficiency, reduced downtime, and safer working environments, they’re confronting several significant obstacles:
- Harsh and hazardous conditions – Workers must inspect hot furnaces, acid regeneration systems, and high-voltage equipment, often in extreme temperatures or exposure to toxic gases.
- Unplanned downtime and production losses – Equipment failures disrupt production lines, leading to high financial losses and decreased product quality.
- Aging workforce and labor shortages – The industry is struggling to find and retain skilled inspectors, creating operational gaps.
To stay competitive and ensure long-term sustainability, metal manufacturers are turning to autonomous inspection robots to optimize operations.
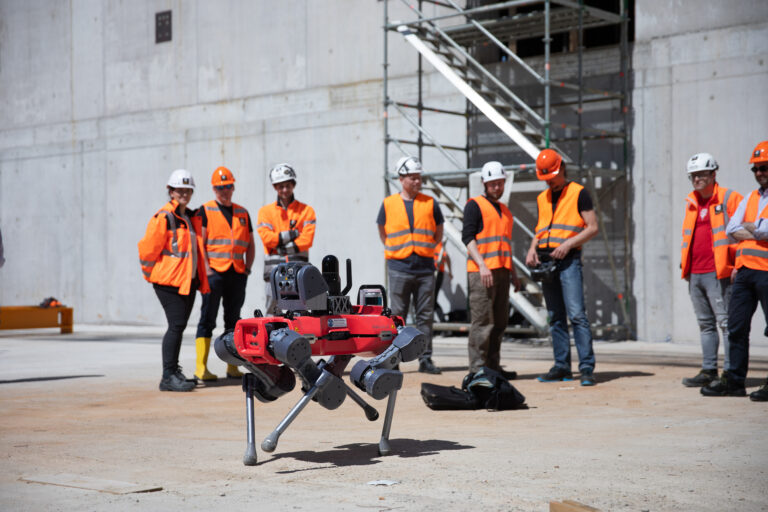
What Is an Inspection Robot, and How Does It Work?
An inspection robot is an autonomous solution designed to perform asset condition monitoring in industrial environments. Unlike fixed sensors or drones, robots like ANYmal provide continuous, repeatable, and high-precision inspections without human intervention.
Key Features of Autonomous Inspection Robots
- 24/7 monitoring – Robots collect data in real time, detecting potential failures before they lead to breakdowns.
- Autonomous navigation – Unlike manually controlled robots, these systems can navigate dynamic environments without obstructing operations.
- Multi-sensor capability – Equipped with thermal cameras, ultrasonic microphones, and gas sensors, robots can detect leaks, temperature changes, and abnormal vibrations.
- Seamless data integration – Inspection results are directly fed into plant management systems, enabling data-driven maintenance decisions.
By automating inspections, manufacturers eliminate human error, reduce safety risks, and increase operational uptime—leading to substantial cost savings and enhanced productivity.
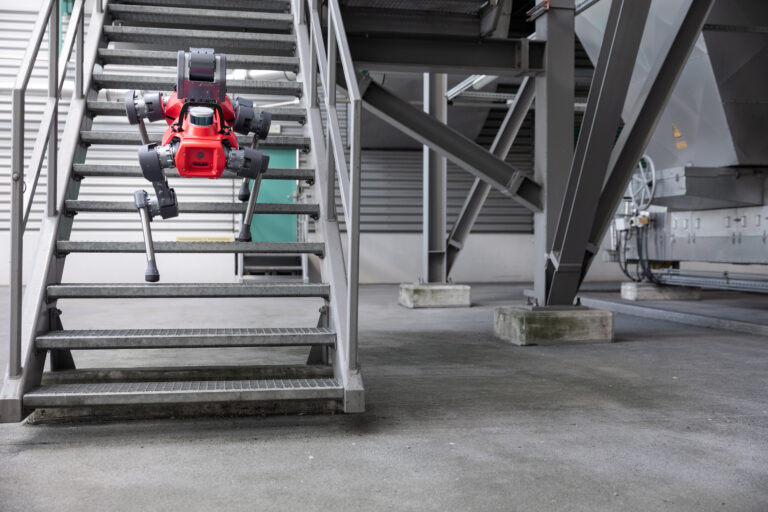
How Inspection Robots Solve the Biggest Challenges in Metal Plants
1. Enhancing Worker Safety in Hazardous Environments
The metal industry is among the most hazardous sectors, with risks ranging from molten metal splashes to toxic gas exposure. Manual inspections force operators to enter dangerous zones, increasing the likelihood of accidents. Many major metal industry leaders, like Outokumpu, have made safety a top priority in their future vision.
How robot improved safety:
- Inspection robots operate in hazardous areas without putting workers at risk and without halting production.
- Thermal cameras and gas sensors detect leaks and overheating before they become dangerous.
- Remote operation and telepresence allow workers to monitor inspections from a safe distance.
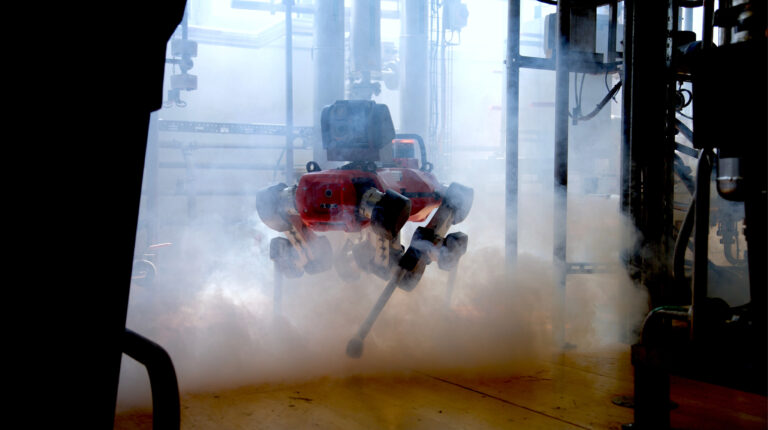
On-Demand Webinar:
Learn How ANYmal Enhances Safety in the Metal Industry:
2. Reducing Downtime with Predictive Maintenance
Unplanned downtime in metal production costs millions in lost revenue each year. Meanwhile, manual inspections only detect problems after they occur, forcing operators to react rather than prevent failures.
How robots optimize maintenance:
- Continuous asset monitoring helps predict failures before they cause downtime.
- Real-time insights allow maintenance teams to take proactive action and support predictive maintenance.
- Consistent, automated inspections eliminate the variability of human assessments.
3. Addressing the Labor Shortage and Aging Workforce
Manufacturing industries are facing a global workforce crisis, with skilled operators retiring and fewer young professionals entering the field. This shortage increases operational strain, thereby decreasing wrench time and reducing plant efficiency.
How robots help bridge the labor gap:
- Handle repetitive inspections to allow human workers to focus on higher-value tasks.
- Provide standardized data collection to remove subjectivity from manual inspections.
- Enable remote supervision to allow fewer workers to manage larger areas.
- By integrating inspection robots, manufacturers future-proof their operations, ensuring reliability, consistency, and long-term efficiency.
By integrating inspection robots, manufacturers future-proof their operations, ensuring reliability, consistency, and long-term efficiency.
How to Get Started with Inspection Robots in Metal Plants
If you’re considering integrating autonomous inspections into your metal facility, here’s what to expect:
Step 1: Define Your Inspection Needs
- Identify critical assets that require continuous monitoring (e.g., furnaces, pumps, cooling systems)
- Evaluate safety risks and determine where robots can replace manual inspections.
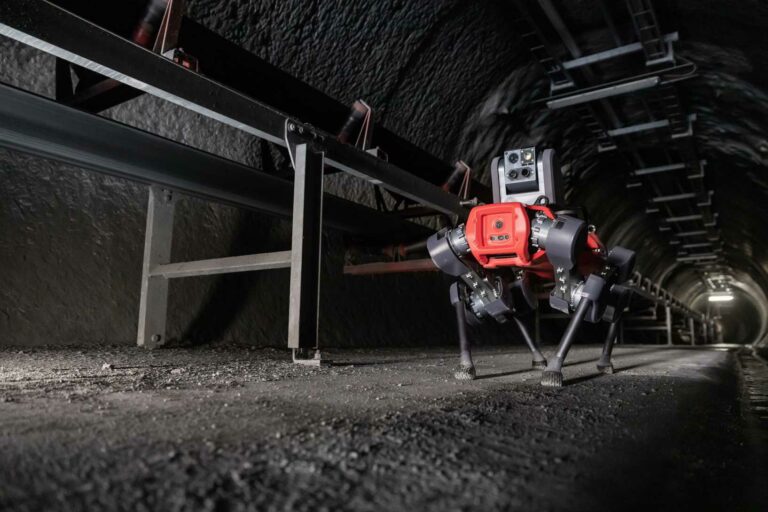
Step 2: Choose the Right Inspection Robot
- Look for rugged, industrial-grade robots that withstand harsh environments.
- Ensure the robot has multi-sensor capabilities for thermal, acoustic, and gas detection.
- Consider data integration features to connect inspections with existing systems.
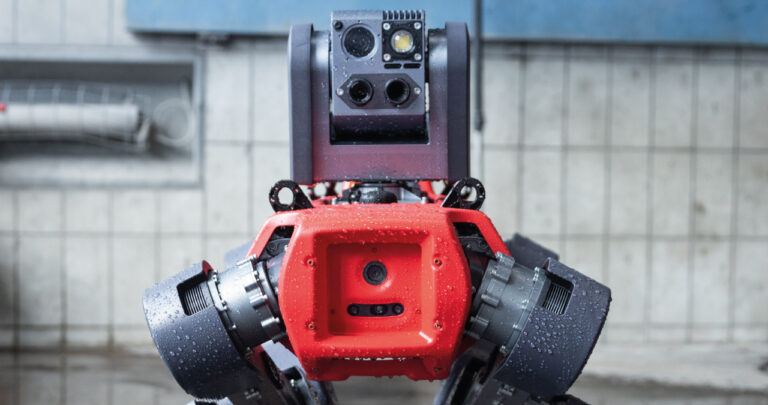
Step 3: Onboard and Train Your Team
- Implement an inspection strategy to maximize robot efficiency.
- Train maintenance teams to interpret robotic inspection data.
- Use predictive maintenance insights to optimize operations.
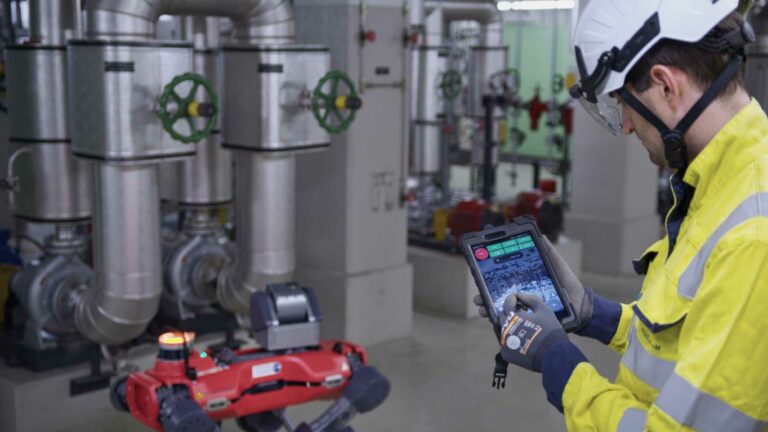
The Future Robotic Inspections in the Metal Industry
The shift toward inspection robots in the metal industry is not just about convenience—it’s about safety, efficiency, and long-term competitiveness. It’s about protecting your revenue now and in the future.
As the industry evolves, automation will play a key role in ensuring operational success. Inspection robots like ANYmal are leading this transformation, enabling metal producers to meet growing demands while staying ahead of safety regulations and workforce challenges.
Book a consultation with our experts today: